La Zona Afectada por el Calor (ZAC) o Heat-Affected Zone (HAZ) en inglés, es una región crítica en las estructuras metálicas soldadas que puede influir en la integridad y la vida útil de una pieza. En este artículo, explicaremos qué es la ZAC, por qué es importante y qué debemos tener en cuenta al trabajar con materiales que experimentan cambios en esta zona.
¿Qué es la Zona Afectada por el Calor (ZAC)?
La Zona Afectada por el Calor es la región del material base que rodea la soldadura y se ha visto afectada térmicamente por el proceso de soldadura, pero no ha sido fundida. El calor generado durante la soldadura puede provocar cambios microestructurales y metalúrgicos en esta área, lo que puede afectar las propiedades mecánicas y la resistencia a la corrosión del material.
La ZAC se puede dividir en varias subregiones, que incluyen:
- Zona de grano grueso: Esta zona está más cerca de la soldadura y experimenta las temperaturas más altas. Aquí, los granos del material base pueden crecer, lo que puede reducir la resistencia a la tracción y la tenacidad.
- Zona de grano fino: Esta zona se encuentra más alejada de la soldadura y experimenta temperaturas más bajas que la zona de grano grueso. La formación de granos más finos en esta área puede mejorar la resistencia y la tenacidad del material.
- Zona intercrítica: Esta zona experimenta temperaturas intermedias y puede experimentar transformaciones de fase parciales. Los cambios en la microestructura pueden afectar las propiedades mecánicas y la resistencia a la corrosión en esta región.
Importancia de la ZAC
La importancia de la Zona Afectada por el Calor radica en su impacto en las propiedades mecánicas y la resistencia a la corrosión del material base. Los cambios en la microestructura y las propiedades del material en la ZAC pueden influir en la resistencia y la vida útil de la pieza soldada. Algunos problemas comunes asociados con la ZAC incluyen:
- Agrietamiento: La ZAC puede ser susceptible a diversos tipos de agrietamiento, como el agrietamiento en frío o el agrietamiento inducido por hidrógeno. Estos problemas pueden comprometer la integridad de la estructura y provocar fallas prematuras.
- Resistencia reducida: Los cambios en la microestructura en la ZAC pueden reducir la resistencia a la tracción y la tenacidad del material, lo que puede aumentar el riesgo de fallas mecánicas.
- Corrosión acelerada: Las modificaciones en la microestructura y la composición química en la ZAC pueden aumentar la susceptibilidad del material a la corrosión, lo que puede reducir la vida útil de la pieza.
Consideraciones al trabajar con la ZAC
Para minimizar los problemas asociados con la Zona Afectada por el Calor, es esencial tener en cuenta lo siguiente:
- Selección de material: Elegir materiales con baja susceptibilidad a los cambios en la ZAC, como aceros de baja aleación y aceros inoxidables austeníticos, puede ayudar a mejorar la resistencia y la vida útil de las piezas soldadas.
- Pre-calentamiento: El pre-calentamiento de las piezas antes de soldar puede reducir la velocidad de enfriamiento y minimizar los cambios abruptos en la microestructura en la ZAC.
- Control del aporte térmico: Mantener un aporte térmico mínimo y constante durante la soldadura puede ayudar a reducir la extensión de la ZAC y limitar los cambios en la microestructura.
- Post-calentamiento y tratamientos térmicos: Realizar tratamientos térmicos después de la soldadura, como el alivio de tensiones o el recocido, puede ayudar a mejorar las propiedades mecánicas y reducir la susceptibilidad al agrietamiento y la corrosión en la ZAC.
En resumen, la Zona Afectada por el Calor es un aspecto crítico en las estructuras soldadas que puede influir en la resistencia y la vida útil de la pieza. Comprender la importanciade la ZAC y tener en cuenta las consideraciones mencionadas al trabajar con materiales que experimentan cambios en esta zona es esencial para garantizar la integridad y el rendimiento a largo plazo de las estructuras soldadas en diversas industrias.
Estructura ZAT de soldadura
Una ZAT típica en un acero al carbono se puede dividir en cuatro regiones distintas según la temperatura máxima alcanzada. Estas regiones junto con el diagrama de fase hierro-carbono pertinente se muestran en el siguiente diagrama.
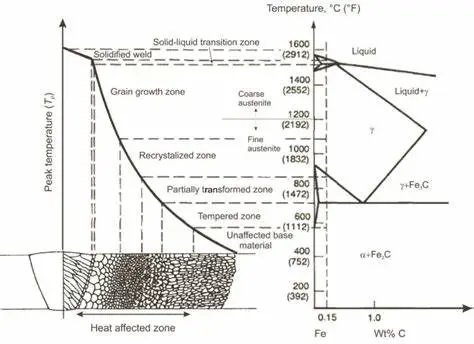
ZAT Región 1 (Zona de crecimiento de grano):
La región 1, que se encuentra en contacto con la línea de fusión, se calentó a una temperatura alta, en el rango de temperatura de la austenita y, por lo tanto, tiene un grano extremadamente grueso.
Normalmente es una zona de alta dureza y, si la velocidad de enfriamiento es lo suficientemente alta, puede transformarse fácilmente en martensita quebradiza. Esta es el área potencialmente más peligrosa de la ZAT.
ZAT Región 2 (Zona de recristalización)
La Región 2 se calentó ligeramente por encima de A 3 en el rango completamente austenítico. Normalmente es de grano fino, de dureza moderada y no es probable que se transforme en martensita.
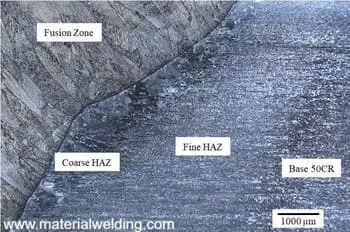
ZAT Región 3 (Zona parcialmente transformada)
La Región 3 se calentó entre A 2 y A 3 , es decir, parcialmente, en el rango austenítico y por lo tanto adquiere una estructura mixta.
Se puede formar una pequeña cantidad de martensita si la velocidad de enfriamiento es lo suficientemente alta. Por lo general, no es muy duro y, sin embargo, puede ser quebradizo si hay martensita presente.
ZAT Región 4 (Zona templada)
La Región 4 no se calentó lo suficientemente alto como para formar martensita, pero el calor de la soldadura ha servido para templar el metal a una condición blanda.
Factores que controlan la microestructura de la ZAT
La microestructura ZAT, está determinada por la composición del acero y el ciclo térmico de soldadura.
Cuanto mayor sea el contenido de carbono, más dura y más susceptible al agrietamiento será la microestructura transformada de la ZAT.
Un mayor contenido de elementos de aleación aumentará la templabilidad, lo que permitirá que se forme más fácilmente una ZAT endurecida; los elementos de aleación particulares también pueden influir en la susceptibilidad al agrietamiento.
El factor total de carbono y los elementos de aleación se puede expresar como equivalente de carbono, que viene dado por la siguiente fórmula
CE = C + Mn/6 + (Cr+Mo+V)/5 + (Ni+Cu)/15
La tasa de enfriamiento de la ZAT depende del espesor de la placa, que se suelda (cuyo aumento aumenta la tasa de enfriamiento), el tamaño del cordón de soldadura (entrada de energía del proceso) y la temperatura de precalentamiento (un aumento en ambos disminuirá la tasa de enfriamiento).
ZAT Dureza
La dureza de la ZAT suele ser un buen indicador de la presencia de martensita y, por tanto, de posibles fisuras. De manera general, se puede afirmar que el agrietamiento rara vez ocurre cuando la dureza HAZ es de 250 HV o menos, pero es común cuando el HV se acerca a 450.
La dureza máxima que se puede tolerar en la ZAT sin agrietamiento inducido por hidrógeno en determinadas condiciones de soldadura se denomina dureza crítica.
Para los aceros estructurales al carbono-manganeso, se ha sugerido una dureza crítica de 350 HV al soldar con electrodos de rutilo y de 400 HV con electrodos básicos bien secos controlados por hidrógeno.
Suponga que realizó tres soldaduras en una placa de acero al 0,25 % C de 25 mm de espesor que se sometió a tres regímenes térmicos diferentes.
La primera soldadura se realizó sin precalentamiento y utilizando una tasa de entrada de calor baja , por lo que es propensa a la formación de martensita dura en la ZAT. Puede esperar una dureza en el rango de 250 VHN.
La segunda soldadura se realizó con suficiente precalentamiento para reducir la velocidad de enfriamiento y eliminar la martensita. Puede esperar una dureza en el rango de 220-230 VHN.
La tercera placa se soldó con precalentamiento y también se postcalentó a 600 °C para duplicar la operación de alivio de tensión. Puede esperar una dureza en el rango de menos de 200 VHN.
Los valores de dureza para las tres zonas de cada soldadura hablan de las microestructuras favorables y desfavorables formadas en cada caso.