Según la norma UNE EN 10020:2001, el acero se define como aquel material en el que el hierro es el elemento predominante, con un contenido de carbono generalmente inferior al 2% y otros elementos adicionales.
El contenido de carbono en el acero tiene un impacto significativo en sus propiedades mecánicas, como resistencia a la tracción, tenacidad y ductilidad. Dependiendo de su composición, el acero se clasifica en diferentes tipos.
Diagrama Tensión-Deformación
El diagrama tensión-deformación es una representación gráfica del ensayo de tracción realizado en el acero. Durante este ensayo, se somete una probeta de acero normalizada a un esfuerzo creciente hasta que se rompe.
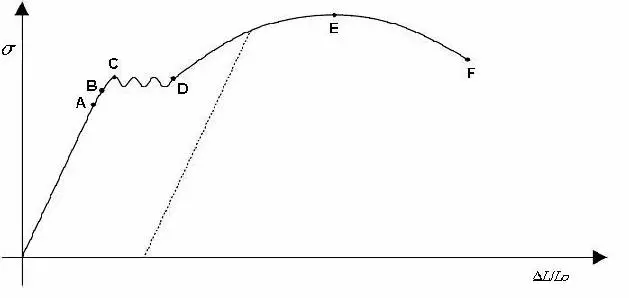
Este ensayo permite obtener información sobre las propiedades mecánicas del acero, como el límite elástico y la resistencia a la tracción.
El diagrama tensión-deformación se obtiene mediante la representación gráfica de un ensayo de tracción normalizado según UNE-EN 10002-1. Este ensayo consiste en aplicar una fuerza de tracción creciente a una probeta de acero normalizada hasta que se rompa. A través del ensayo de tracción se pueden calcular diversas propiedades mecánicas del acero.
La probeta de acero utilizada en el ensayo es una pieza cilíndrica cuyas dimensiones se relacionan de la siguiente manera:
- L0 = 5,65 · √S0
En el ensayo de tracción del acero, las variables anteriores pueden tener los siguientes valores:
- Si D0 = 20 mm, entonces L0 = 100 mm.
- O si D0 = 10 mm, entonces L0 = 50 mm.
Límite elástico y Resistencia a la tracción
El límite elástico es el punto en el que el acero deja de comportarse elásticamente y comienza a deformarse permanentemente. Por otro lado, la resistencia a la tracción es la carga máxima que el acero puede soportar antes de romperse. Estas propiedades son fundamentales para el diseño y la evaluación de estructuras y componentes de acero.
Para determinar las propiedades mecánicas del acero, como el límite elástico (fy), la resistencia a la tracción (fu) y otras características mecánicas como el módulo de elasticidad (E) o el alargamiento máximo en la rotura, se utiliza el ensayo de tracción normalizado en la UNE-EN 10002-1.
La resistencia a la tracción se calcula a partir de este ensayo y se define como la máxima carga que provoca la rotura del material por tracción, dividida por el área de la sección transversal inicial de la probeta. Por otro lado, el límite elástico marca el punto en el que el material comienza a deformarse plásticamente una vez superado dicho límite. En el apartado de anexos de este tutorial se pueden encontrar los valores de límite elástico y resistencia a la tracción para diferentes calidades de acero según las normativas europea y americana.
A continuación se adjunta una tabla con los valores de resistencia a la tracción, límite elástico y dureza según la norma americana AISI:
Calidad de acero | Resistencia a la tracción (fu) | Límite elástico (fy) | Dureza |
---|---|---|---|
Acero A | 500 MPa | 300 MPa | 55 |
Acero B | 600 MPa | 400 MPa | 60 |
Acero C | 700 MPa | 500 MPa | 65 |
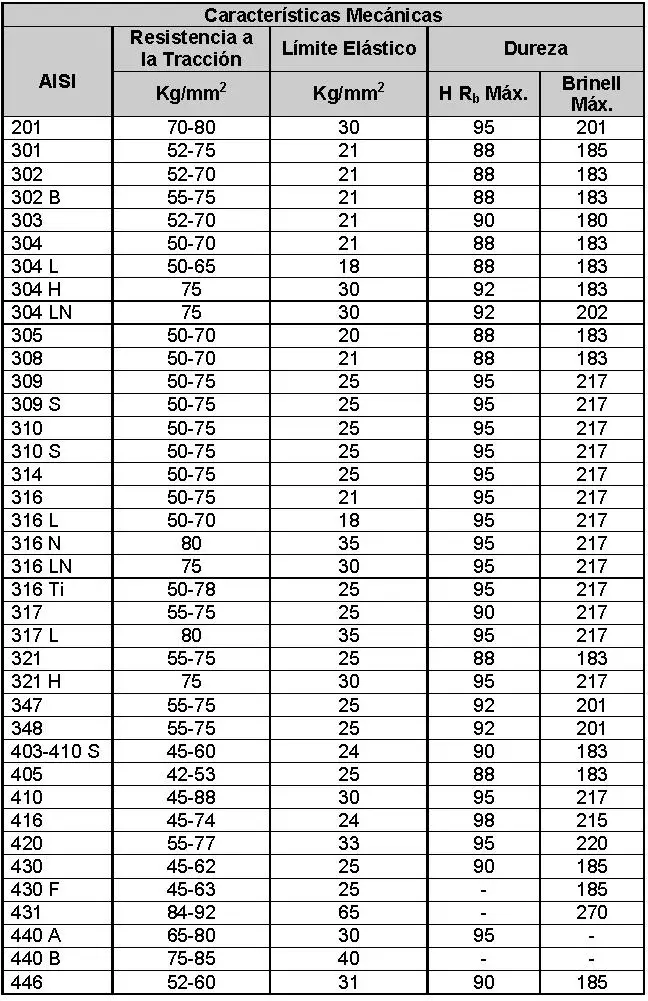
Módulo de elasticidad longitudinal o Módulo de Young
El módulo de elasticidad longitudinal, también conocido como módulo de Young, es una medida de la rigidez del acero. Indica cómo responde el acero a una carga en términos de deformación elástica.
El módulo de Young es una constante para cada material y se utiliza en el cálculo de estructuras y componentes de acero.
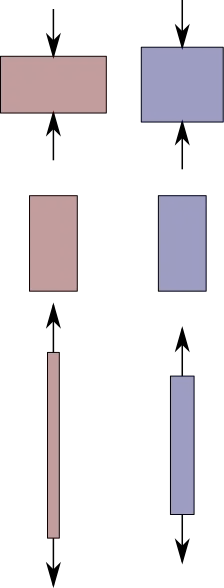
Para comprender el funcionamiento de los ensayos de tracción y aprovechar al máximo las capacidades de la máquina universal, es importante familiarizarse con los métodos utilizados para lograr nuestros objetivos de manera óptima.
En el caso del módulo de Young, su denominación se debe al científico Thomas Young, quien estudió este concepto durante el siglo XIX. Sin embargo, el método fue desarrollado originalmente en 1727 por Leonhard Euler, y su forma actual se implementó en 1782 cuando Giordani Riccati llevó a cabo los primeros experimentos.
El módulo de Young, también conocido como módulo de elasticidad longitudinal, es un parámetro que revela el comportamiento de un material elástico en relación con el tipo de fuerza aplicada y el consiguiente cambio en la longitud del material. Su objetivo es establecer la relación entre la tensión ejercida sobre un objeto en su eje longitudinal y la deformación medida en ese mismo eje. De esta manera, el módulo de Young mide el comportamiento elástico de un material y también permite predecir su capacidad de estiramiento.
La fórmula utilizada para calcular el módulo de Young es la siguiente:
- E = σ / ε
Donde:
- E representa el módulo de Young, medida en pascal (Pa).
- σ es la tensión uniaxial o la fuerza uniaxial por unidad de área, también medida en pascal (Pa).
- ε es la deformación o cambio de longitud dividido por la longitud original, una cantidad adimensional.
Esta fórmula establece una relación entre la tensión aplicada a un material y la deformación resultante. El módulo de Young proporciona información sobre la rigidez de un material, indicando cómo responde ante la aplicación de fuerza y cómo se deforma elásticamente. Un mayor valor de módulo de Young indica una mayor rigidez del material.
Módulo de elasticidad transversal
El módulo de elasticidad transversal es otra propiedad relacionada con la deformación elástica del acero. Representa la resistencia del acero a deformarse en dirección perpendicular a la carga aplicada. Esta propiedad es relevante en aplicaciones donde el acero está sujeto a fuerzas de corte o torsión.
El módulo de elasticidad transversal, también conocido como módulo de elasticidad al cortante, es un parámetro intrínseco de cada material que describe la relación entre la tensión cortante y la deformación angular en el material.
La fórmula para calcular el módulo de elasticidad transversal (G), también conocido como módulo de rigidez o módulo de elasticidad al cortante, es la siguiente:
- G = τ / γ
Donde:
- G representa el módulo de elasticidad transversal, medido en pascal (Pa).
- τ es la tensión cortante, medida en pascal (Pa).
- γ es la deformación angular o deformación cortante, una cantidad adimensional.
Coeficiente de Poisson
El coeficiente de Poisson es una medida de la deformación lateral que experimenta el acero cuando se somete a una carga axial. Indica cómo se contrae o expande el acero en dirección perpendicular a la carga aplicada. El coeficiente de Poisson es importante en el diseño y la predicción del comportamiento estructural del acero.
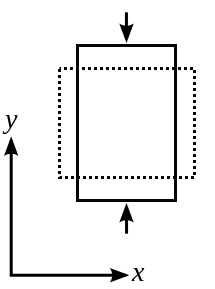
El coeficiente de Poisson (representado por la letra griega ν) es una constante elástica que indica el grado de contracción de una sección de un prisma de material elástico lineal e isótropo cuando se estira en dirección longitudinal y se adelgaza en direcciones perpendiculares al estiramiento. Este coeficiente recibe su nombre en honor al físico francés Simeon Poisson.
La mayoría de los materiales tienen valores de coeficiente de Poisson que oscilan entre 0,0 y 0,5. En el caso de materiales blandos, como el caucho, donde el módulo aparente es mucho mayor que el módulo de cizallamiento, el coeficiente de Poisson tiende a ser cercano a 0,5. Por otro lado, en las espumas de polímero de célula abierta, el coeficiente de Poisson es cercano a cero debido a que las células tienden a colapsar en compresión. En general, muchos sólidos típicos presentan coeficientes de Poisson en el rango de 0,2 a 0,3.
Estricción
La estricción es la reducción de la sección transversal de la probeta de acero justo antes de la rotura. Este fenómeno ocurre debido a la localización de la deformación en una zona específica de la probeta. La estricción es importante para comprender el comportamiento del acero bajo cargas extremas y puede afectar la resistencia y la ductilidad del material.
Resiliencia
La resiliencia es la capacidad del acero para absorber energía durante la deformación elástica y liberarla cuando se retira la carga. Es una medida de la tenacidad y la capacidad de resistir impactos. La resiliencia es especialmente relevante en aplicaciones donde el acero está expuesto a cargas dinámicas y choques.
Tenacidad a la fractura
La tenacidad a la fractura es la capacidad del acero para resistir la propagación de grietas y fracturas. Es una propiedad crucial en la seguridad estructural, ya que un material tenaz puede absorber energía y evitar la propagación de fallas catastróficas.
Dureza Brinell
La dureza Brinell es una medida de la resistencia del acero a la penetración. Se determina aplicando una carga estática a una esfera de acero endurecido y midiendo la huella resultante. La dureza Brinell se utiliza para evaluar la resistencia al desgaste y la capacidad de endurecimiento del acero.
Soldabilidad
La soldabilidad del acero se refiere a su capacidad para unirse mediante soldadura. Algunos aceros son más fáciles de soldar que otros debido a su composición química y características microestructurales.
La soldabilidad del acero se evalúa teniendo en cuenta factores como la compatibilidad de los materiales base, la preparación adecuada de las superficies a soldar, la selección del proceso de soldadura adecuado y la aplicación de técnicas de soldadura correctas.
Conclusiones
En resumen, las características mecánicas del acero desempeñan un papel fundamental en su rendimiento y aplicaciones.
El conocimiento de estas propiedades es esencial para los ingenieros y profesionales que trabajan con acero, ya que les permite diseñar estructuras seguras y eficientes, seleccionar el tipo de acero adecuado para cada aplicación y evaluar su resistencia y durabilidad.
Desde el límite elástico y la resistencia a la tracción hasta el módulo de elasticidad y la tenacidad a la fractura, cada una de estas características mecánicas proporciona información valiosa sobre el comportamiento del acero bajo diferentes condiciones de carga. Comprender y utilizar estas propiedades de manera efectiva permite aprovechar al máximo las ventajas del acero como material estructural.