Ajustes y Tolerancias
En cualquier proceso de fabricación mecánica, es esencial utilizar planos y representaciones gráficas para las piezas y componentes que se van a fabricar.
Sin embargo, es importante tener en cuenta que las dimensiones reales de las piezas a menudo no están completamente definidas en los planos y acotaciones, ya que siempre habrá una discrepancia entre las medidas teóricas o exactas que se muestran en los planos y las medidas reales de las piezas.
Estas discrepancias pueden deberse a varios factores, entre los cuales se destacan:
- La presencia de juegos y holguras en las herramientas o máquinas utilizadas.
- Errores en los instrumentos de medición o en las personas que realizan las mediciones.
- La dilatación o deformación de las piezas debido a las temperaturas que experimentan durante los procesos de mecanizado y fabricación.
- Deformaciones causadas por tensiones internas que se generan en las piezas.
A continuación se muestra una tabla que ejemplifica los errores comunes que pueden ocurrir con diferentes tipos de máquinas durante el proceso de fabricación de piezas. Estos datos también proporcionan una aproximación de la precisión que se puede lograr con dichas máquinas.
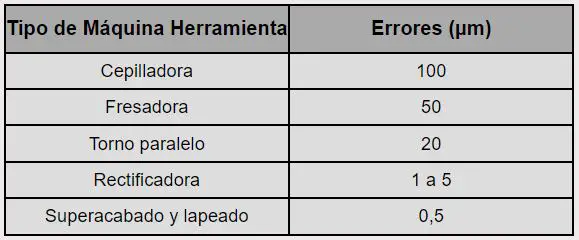
Es evidente que cuanto más cuidadosa sea la fabricación, utilizando herramientas de alta precisión, controlando la temperatura durante el mecanizado y contando con operarios experimentados, menor será la diferencia entre la medida real de la pieza y el valor teórico indicado en el plano.
No obstante, siempre habrá alguna discrepancia, por mínima que sea, al obtener una pieza con una determinada medida. Dependiendo de la importancia y el impacto que tenga esta medida en el resultado final, se pueden distinguir dos tipos:
- Cota funcional: es aquella medida crucial para el funcionamiento de la pieza, es decir, afecta directamente al mecanismo. Si se comete un error excesivo en esta medida, las piezas pueden resultar inutilizables.
- Cotas auxiliares o no funcionales: son aquellas medidas en las que las diferencias entre las medidas reales y las nominales o teóricas no tienen relevancia o importancia significativa.
Tolerancia de fabricación
La tolerancia permitida, que se refiere principalmente a las dimensiones de un elemento a fabricar, también puede incluir la forma y posición de las superficies que lo limitan. Esto se debe a que, como se mencionó anteriormente, una superficie mecanizada nunca será completamente plana, cilíndrica, circular o esférica.
Además, incluso con mecanizados precisos, no es posible lograr superficies perfectamente paralelas, perpendiculares o coaxiales entre sí.
Por ejemplo, no se puede obtener una perpendicularidad perfecta entre caras adyacentes de un cubo, ya sea que se mecanice a mano o con una máquina, ni un paralelismo perfecto entre sus caras opuestas.
Tampoco es posible obtener en un torno, e incluso en una rectificadora, una pieza cilíndrica con generatrices perfectamente paralelas entre sí. Por lo tanto, se deben aceptar:
- Tolerancias dimensionales.
- Tolerancias geométricas de forma y posición.
Además, teniendo en cuenta los errores inevitables en la medición de las piezas, estas tolerancias deben reducirse para garantizar que todas las piezas cumplan con las dimensiones del plano, de modo que se pueda esperar que su funcionamiento sea conforme a lo previsto.
Definiciones
Las normas UNE 4024, 4026 y 5023, que se basan en el sistema de tolerancias de la norma ISO 286 ampliamente aceptada, establecen los símbolos, designaciones y definiciones que utilizaremos. Estas definiciones se aplican al acoplamiento de piezas cilíndricas, como ejes y agujeros, pero también pueden aplicarse a elementos de cualquier otra forma. La temperatura de referencia para las dimensiones es de 20 ºC.
Construcciones mecánicas. Ajustes (acoplamientos)
En las construcciones mecánicas, generalmente hay una cadena más o menos compleja de elementos acoplados, ya sean móviles o no, donde cada uno se conecta al siguiente. Esta cadena comienza en el bastidor, que es el soporte de todos los mecanismos, y se cierra sobre sí misma.
Los elementos acoplados más simples y comunes son un eje en funcionamiento y su correspondiente alojamiento, es decir, un agujero. El acoplamiento puede ser móvil, lo que significa que hay un espacio radial (juego) entre el eje y el agujero que permite el movimiento relativo de rotación y traslación, y también permite la presencia de una película lubricante.
Por otro lado, el acoplamiento puede ser forzado, lo que significa que el eje se fija al agujero mediante una fuerza que elimina el movimiento relativo entre ambos, quedando unidos de forma sólida. Para lograr esto, el diámetro del eje debe ser mayor que el del agujero antes del acoplamiento (interferencia o aprieto). En este caso, el montaje es posible mediante cambios de temperatura en una o ambas piezas, o debido a la deformación plástica y elástica de los dos elementos acoplados, lo que genera un enlace rígido y permanente.
Las piezas ajustadas son aquellas que se acoplan entre sí, ya sea articuladas o no, formando un vínculo. Dependiendo de las dimensiones de ambas piezas, pueden haber ajustes con juego (cuando el eje es menor que el agujero) o ajustes con aprieto (cuando el eje es mayor que el agujero antes del montaje).
Es importante que el tipo de acoplamiento mantenga sus características durante el funcionamiento variable del mecanismo, que puede involucrar cargas dinámicas variables o repentinas, cambios en el número de revoluciones, variaciones en las propiedades del lubricante, cambios de temperatura, entre otros.
Los dos tipos de ajustes mencionados se logran estableciendo límites máximo y mínimo en las dimensiones de cada elemento a acoplar. El diseñador debe prever la magnitud de estas diferencias basándose en normas de ajuste o, en algunos casos, en su propia experiencia. La diferencia entre estos límites se conoce como tolerancia de fabricación de cada elemento.
Tolerancia dimensional
Las definiciones relacionadas con los conceptos de eje y agujero, así como las medidas y tolerancias asociadas, son las siguientes:
- Eje: Es una pieza en forma cilíndrica o prismática que se acopla dentro de otra. Puede tener forma de prisma, que es un poliedro con dos bases paralelas e iguales y caras laterales en forma de paralelogramos. Aunque la mayoría de los ejes son cilíndricos, no es necesario que sean de revolución.
- Agujero: Es el alojamiento del eje, es decir, la cavidad en la que se inserta el eje.
- Medida nominal (ejes: d / agujeros: D): Es el valor indicado en planos o especificaciones para una medida determinada. Para ejes se utiliza la variable d, mientras que para agujeros se utiliza la variable D.
- Cota efectiva o real: Es la medida real que tiene la pieza una vez terminada.
- Tolerancia dimensional (ejes: t / agujeros: T): Es la diferencia entre la medida máxima y la mínima permitida para la fabricación de la pieza real. En cualquier proceso de fabricación, siempre existen discrepancias entre las cotas nominales y efectivas. La tolerancia dimensional establece el margen de error permitido.
- Para ejes, la tolerancia dimensional se calcula como t = dmáx – dmín, donde dmáx y dmín son las medidas máxima y mínima permitidas en el diámetro del eje.
- Para agujeros, la tolerancia dimensional se calcula como T = Dmáx – Dmín, donde Dmáx y Dmín son las medidas máxima y mínima permitidas en el diámetro del agujero.
- Cotas máxima y mínima: Son las medidas máxima y mínima permitidas en una pieza determinada. Por ejemplo, en el caso de los diámetros permisibles del agujero, Dmáx = D + Tsup y Dmín = D – Tinf, donde D es la cota nominal o medida del diámetro del agujero.
- Diferencia superior (Tsup): Representa la diferencia entre la cota máxima y la nominal.
- Diferencia inferior (Tinf): Es la diferencia entre la cota nominal y la mínima.

En el ejemplo proporcionado, se especifica una cota nominal de 40 mm para el diámetro del agujero. Utilizando las definiciones anteriores, podemos calcular las cotas máxima, mínima y la tolerancia:
- Cota máxima: Se obtiene sumando la desviación superior a la cota nominal. En este caso, la desviación superior es de +0,2 mm. Por lo tanto, la cota máxima sería 40 + 0,2 = 40,2 mm.
- Cota mínima: Se obtiene restando la desviación inferior a la cota nominal. En este caso, la desviación inferior es de -0,1 mm. Por lo tanto, la cota mínima sería 40 – 0,1 = 39,9 mm.
- Tolerancia (t): Se calcula como la diferencia entre la cota máxima y la cota mínima. En este caso, sería 40,2 – 39,9 = 0,3 mm.
Por lo tanto, en este ejemplo, la cota máxima sería 40,2 mm, la cota mínima sería 39,9 mm y la tolerancia sería de 0,3 mm.
Es importante tener en cuenta que cuando no se especifica una desviación, se sobreentiende que su valor es cero. Por ejemplo, si se indica “30 + 0,2”, se entiende que la desviación inferior es cero.
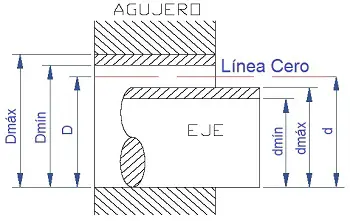
- Ajuste: Se refiere al conjunto de dos piezas, el eje y el agujero, que están diseñadas para acoplarse entre sí de manera precisa. El ajuste se logra cuando el eje se inserta en el agujero, permitiendo un movimiento suave o un ajuste apretado, según los requisitos de la aplicación.
- Juego (J): Es la diferencia entre el diámetro del agujero y el del eje. El juego se refiere al espacio o holgura existente entre el eje y el agujero, permitiendo un movimiento relativo entre ellos. El juego puede variar dependiendo de las tolerancias dimensionales especificadas para el eje y el agujero.
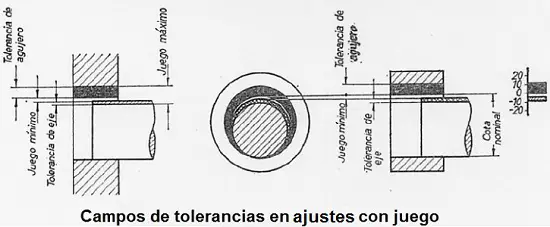
• Juego máximo (Jmáx): Es el espacio máximo permitido entre el eje y el agujero, lo cual representa la diferencia entre el diámetro máximo del agujero y el diámetro mínimo del eje.
- Jmáx = Dmáx – dmín
• Juego mínimo (Jmín): Es el espacio mínimo permitido entre el agujero y el eje, lo cual representa la diferencia entre el diámetro mínimo del agujero y el diámetro máximo del eje.
- Jmín = Dmín – dmáx
• Aprieto (A): Ocurre cuando el diámetro del eje es mayor que el diámetro del agujero, lo que resulta en una “interferencia” entre los diámetros. La diferencia entre estos diámetros se conoce como aprieto.
• Aprieto máximo (Amáx): Es la diferencia entre el diámetro máximo del eje (dmáx) y el diámetro mínimo del agujero (Dmín).
- Amáx = dmáx – Dmín
• Aprieto mínimo (Amín): Es la diferencia entre el diámetro mínimo del eje (dmín) y el diámetro máximo del agujero (Dmáx).
- Amín = dmín – Dmáx
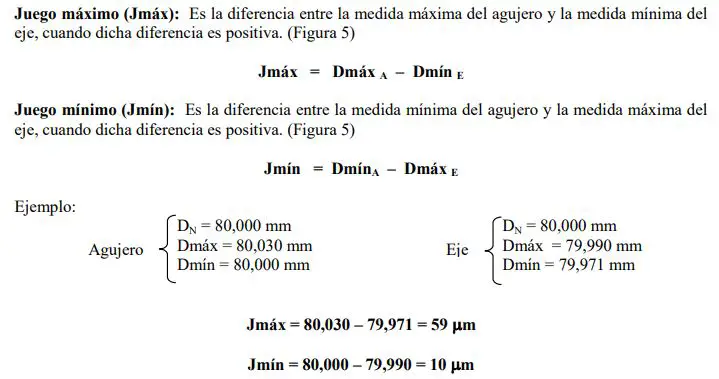
Tolerancias y ajustes según ISO (International Standardization Organization)
Como se ha mencionado anteriormente, no existen máquinas que produzcan piezas idénticas entre sí, ni instrumentos de medición que garanticen una repetibilidad y precisión absolutas en las medidas. Por lo tanto, no es posible obtener medidas absolutas. Tanto la fabricación como la medición están sujetas a diferentes tipos de errores.
Debido a esto, es necesario establecer límites ajustados a las necesidades al obtener cada dimensión. Cuando los límites pueden ser amplios, no se establecen en el diseño y se denominan cotas libres. En general, en el plano se especifican las tolerancias máximas para las dimensiones libres. Por ejemplo, se puede indicar que todas las dimensiones sin tolerancia admiten un margen de ±0,5 mm.
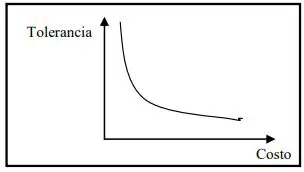
De acuerdo con lo expuesto, existirá un rango máximo y mínimo dentro del cual puede variar la dimensión real de una pieza aceptable, lo cual se conoce como tolerancia. La tolerancia debe ajustarse de manera estricta a las necesidades, ya que si bien una tolerancia más estrecha brinda una mayor garantía de intercambiabilidad, también aumenta significativamente el costo, siguiendo una ley hiperbólica expresada en la Figura 1 cuando el valor de la tolerancia disminuye.
Las Normas ISO 286 establecen:
- Un sistema de tolerancias.
- Un sistema de ajustes.
- Un sistema de calibres límites para la verificación y control de piezas.
Estas normas se aplican a piezas cilíndricas simples, como ejes y agujeros, y pueden extenderse a casos más complejos. A continuación se presentan definiciones extraídas de estas normas (consultar normas fundamentales DIN 7182 en adelante). Cada dimensión recibe una tolerancia de acuerdo con su aplicación.
Las tolerancias pueden referirse a dimensiones y formas (tolerancias macrogeométricas) o a la rugosidad superficial (tolerancias microgeométricas). Estas últimas no están normalizadas por la ISO.