La soldadura es un proceso esencial en diversas industrias, desde la construcción hasta la fabricación de maquinaria. La calidad de las uniones soldadas es fundamental para asegurar la integridad y la seguridad de estructuras y productos finales. Con el fin de lograr este objetivo, se realizan una variedad de pruebas de laboratorio para evaluar la calidad de las soldaduras. En este artículo, exploraremos algunas de las pruebas de laboratorio más comunes utilizadas en el campo de la soldadura.
Ensayo de Tracción
El ensayo de tracción es una prueba mecánica utilizada para determinar las propiedades de resistencia y deformación de un material. Es una de las pruebas más comunes y fundamentales en la ingeniería de materiales y se utiliza para evaluar la calidad y el rendimiento de diversos materiales, como metales, plásticos, cerámicas y materiales compuestos.
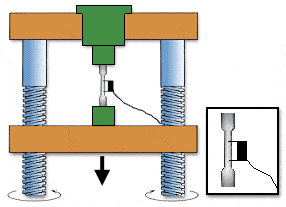
El objetivo principal del ensayo de tracción es determinar la resistencia a la tracción de un material, es decir, la máxima fuerza que puede soportar antes de romperse. Además, también permite evaluar la capacidad del material para deformarse bajo carga y su comportamiento elástico o plástico.
Principio del ensayo
El ensayo de tracción se realiza utilizando una máquina de ensayo llamada máquina universal de ensayos, que aplica una fuerza de tracción gradualmente al material hasta que se produce la rotura. Durante el ensayo, se registran la fuerza aplicada y la deformación resultante, lo que permite trazar una curva de tensión-deformación.
La curva de tensión-deformación proporciona información importante sobre las propiedades mecánicas del material. Al analizar esta curva, se pueden determinar parámetros como el límite elástico, el límite de fluencia, la resistencia máxima y la ductilidad del material.
El ensayo de tracción consiste en aplicar una fuerza de tracción gradual a una muestra de soldadura hasta que se rompa. Se mide la resistencia de la unión soldada y se evalúa la elongación y la reducción de área para determinar la ductilidad del material.
Normas del ensayo
Las normas comunes para el ensayo de tracción son la norma ASTM A370, ASTM E8 para metales y la norma ISO 6892 para la tracción de materiales metálicos.
El ensayo de tracción evalúa la resistencia y la ductilidad de la soldadura. Los requisitos dependen del tipo de material y de las especificaciones del proyecto, y se basan en los estándares establecidos.
Ensayo de Doblez
El ensayo de doblez es una prueba mecánica utilizada para evaluar la ductilidad y la resistencia de un material a la deformación por flexión. Este ensayo es comúnmente utilizado en la industria para determinar la calidad y la idoneidad de materiales como metales, plásticos, cerámicas y materiales compuestos.
El objetivo principal del ensayo de doblez es evaluar la capacidad de un material para soportar cargas aplicadas en forma de flexión sin romperse. Durante el ensayo, se aplica una fuerza en el centro de una muestra de material, lo que provoca una deformación en forma de curvatura. La muestra se dobla hasta que se produce la rotura o hasta que se alcanza un ángulo de flexión predefinido.
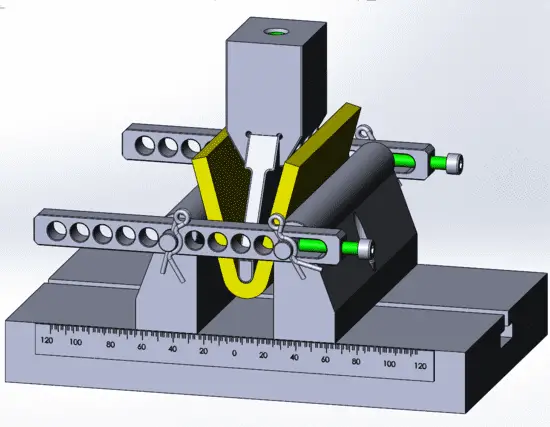
Existen diferentes métodos para realizar el ensayo de doblez, dependiendo del tipo de material y de las normas o estándares aplicables. Algunos de los métodos más comunes incluyen el ensayo de doblez en tres puntos y el ensayo de doblez en cuatro puntos.
En el ensayo de doblez en tres puntos, se coloca la muestra de material sobre dos soportes y se aplica una fuerza en el centro de la muestra mediante un punzón. La muestra se dobla hasta que se produce la rotura o hasta que se alcanza un ángulo de flexión predefinido. Este método permite evaluar la resistencia y la ductilidad del material.
En el ensayo de doblez en cuatro puntos, se colocan dos soportes en los extremos de la muestra y se aplican dos fuerzas en el centro de la muestra mediante dos punzones. Este método proporciona una distribución más uniforme de la carga y permite evaluar la resistencia y la ductilidad del material de manera más precisa.
Principio del ensayo
Durante el ensayo de doblez, se registran la fuerza aplicada y la deformación resultante, lo que permite trazar una curva de carga-deformación. Esta curva proporciona información sobre la capacidad del material para soportar cargas de flexión y su comportamiento ante la deformación.
El ensayo de doblez es ampliamente utilizado en la industria para evaluar la calidad y la idoneidad de materiales en aplicaciones donde la flexión es un factor crítico, como en la fabricación de estructuras, componentes de automóviles, muebles, tuberías, entre otros. También se utiliza para el control de calidad de los materiales, ya que permite detectar posibles defectos o variaciones en las propiedades mecánicas de los materiales.
El ensayo de doblez consiste en aplicar una fuerza de flexión a una muestra de soldadura para evaluar su ductilidad y resistencia. La muestra se dobla hasta que se produzca una fractura o hasta que se alcance un ángulo de flexión específico.
Normas del ensayo
Las normas comunes para el ensayo de doblez incluyen la norma ASTM E190 para metales y la norma ISO 5173 para la flexión de materiales metálicos.
Requisitos del ensayo: El ensayo de doblez evalúa la capacidad de la soldadura para resistir cargas de flexión. Los requisitos varían según el tipo de soldadura y las especificaciones del proyecto.
Ensayo de Impacto
El ensayo de impacto es una prueba mecánica utilizada para evaluar la resistencia de un material a la fractura bajo cargas de impacto repentinas. Este ensayo es comúnmente utilizado en la industria para determinar la tenacidad y la capacidad de absorción de energía de materiales como metales, plásticos, cerámicas y materiales compuestos.
El objetivo principal del ensayo de impacto es simular las condiciones en las que un material puede experimentar una carga de impacto, como golpes, caídas o colisiones. Durante el ensayo, se aplica una fuerza de impacto repentina a una muestra de material mediante un martillo o un péndulo, generando una carga de impacto en un punto específico de la muestra.
Existen diferentes métodos para realizar el ensayo de impacto, dependiendo del tipo de material y de las normas o estándares aplicables. Algunos de los métodos más comunes incluyen el ensayo de impacto Charpy y el ensayo de impacto Izod.
Principio del ensayo
En el ensayo de impacto Charpy, se coloca la muestra de material en una posición horizontal y se aplica una fuerza de impacto en el centro de la muestra mediante un martillo pendular. La muestra se rompe debido a la carga de impacto y se mide la energía absorbida por la muestra antes de la fractura. Esta energía absorbida se utiliza para evaluar la tenacidad del material.
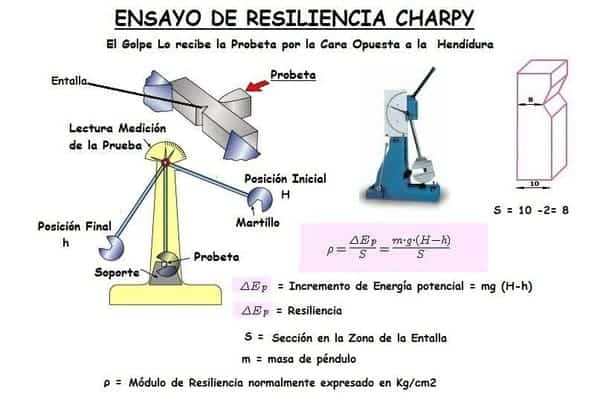
En el ensayo de impacto Izod, se coloca la muestra de material en una posición vertical y se aplica una fuerza de impacto en el extremo de la muestra mediante un martillo pendular. La muestra se rompe debido a la carga de impacto y se mide la energía absorbida por la muestra antes de la fractura. Esta energía absorbida también se utiliza para evaluar la tenacidad del material.
Durante el ensayo de impacto, se registran la energía absorbida y la forma de fractura de la muestra, lo que permite evaluar la capacidad del material para resistir cargas de impacto y su comportamiento ante la fractura. Además, también se pueden realizar análisis metalográficos en la zona de fractura para obtener información adicional sobre la resistencia y la ductilidad del material.
El ensayo de impacto es ampliamente utilizado en la industria para evaluar la calidad y la idoneidad de materiales en aplicaciones donde la resistencia al impacto es un factor crítico, como en la fabricación de estructuras, componentes de automóviles, maquinaria pesada, entre otros. También se utiliza para el control de calidad de los materiales, ya que permite detectar posibles defectos o variaciones en las propiedades mecánicas de los materiales.
El ensayo de impacto mide la capacidad de una soldadura para resistir cargas de impacto repentinas. Se utiliza un dispositivo de impacto para aplicar una fuerza en forma de golpe sobre una muestra de soldadura.
Normas del ensayo
Las normas comunes para el ensayo de impacto son la norma ASTM E23 para materiales metálicos y la norma ISO 148 para la determinación de la tenacidad al impacto de materiales metálicos.El ensayo de impacto evalúa la fragilidad de la soldadura y su capacidad para resistir fracturas bajo condiciones de impacto. Los requisitos dependen del tipo de material y de las especificaciones del proyecto.
Ensayo de Macroestructura
El ensayo de macroestructura es una técnica utilizada para examinar la estructura y la distribución de los componentes de un material a simple vista o con la ayuda de una lupa o un microscopio. Este ensayo se utiliza principalmente en la metalurgia y la metalografía para evaluar la calidad y las propiedades de los materiales metálicos.
El objetivo principal del ensayo de macroestructura es analizar la apariencia y la distribución de las fases, inclusiones, porosidades y otros defectos en un material. Esto proporciona información valiosa sobre la calidad del material, su proceso de fabricación y su comportamiento en servicio.
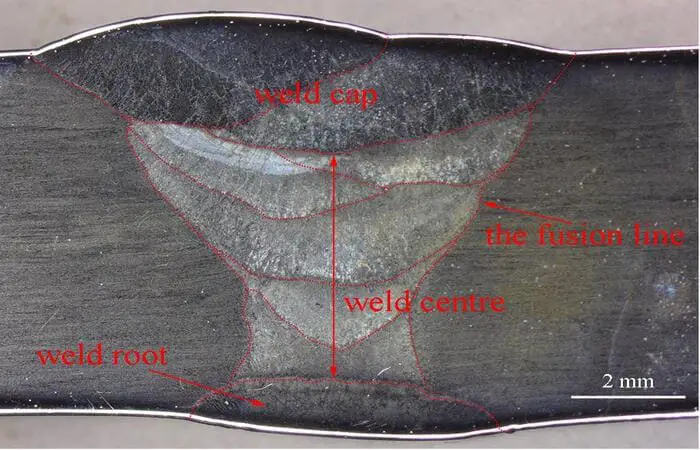
El ensayo de macroestructura se realiza generalmente en muestras representativas del material, que pueden ser secciones transversales de piezas o probetas específicas. Estas muestras se preparan mediante técnicas de corte, pulido y ataque químico para revelar la estructura interna del material.
Una vez preparadas las muestras, se pueden realizar diferentes técnicas de observación para analizar la macroestructura. Estas técnicas incluyen:
- Observación visual: Se realiza a simple vista o con la ayuda de una lupa para examinar la apariencia general del material, como la presencia de inclusiones, porosidades, grietas u otros defectos visibles.
- Observación con lupa: Se utiliza una lupa de aumento para examinar con mayor detalle la estructura del material y detectar características como la distribución de fases, la orientación de los granos y la presencia de defectos.
- Observación con microscopio: Se utiliza un microscopio óptico o un microscopio electrónico de barrido (SEM) para obtener imágenes ampliadas de la estructura del material. Esto permite una evaluación más precisa de la distribución de fases, la morfología de los granos y la presencia de defectos a nivel microscópico.
El ensayo de macroestructura proporciona información importante sobre la calidad y las propiedades del material. Permite detectar defectos, como inclusiones no metálicas, segregaciones, fisuras o porosidades, que pueden afectar la resistencia, la ductilidad y otras propiedades mecánicas del material. También puede revelar información sobre el proceso de fabricación, como la presencia de tratamientos térmicos, la dirección de solidificación o la presencia de zonas afectadas por el calor.
Principio del ensayo
El ensayo de macroestructura consiste en cortar una sección transversal de una soldadura y examinarla a través de un microscopio o lupa. Permite evaluar la calidad de la soldadura, identificar defectos como inclusiones, fisuras o falta de fusión, y determinar si la estructura de la soldadura cumple con los estándares establecidos.
- Normas del ensayo: No existe una norma específica para el ensayo de macroestructura, pero se pueden seguir las directrices establecidas por organizaciones como AWS (American Welding Society) AWS D1.1 o ISO (International Organization for Standardization) ISO 15614.
- Requisitos del ensayo: El ensayo de macroestructura permite una evaluación visual de la calidad de la soldadura y la detección de posibles defectos. Los requisitos dependen de los estándares establecidos y las especificaciones del proyecto.
Análisis de Composición Química
El análisis de composición química es una técnica utilizada para determinar la cantidad y la proporción de los elementos químicos presentes en una muestra de material. Este análisis es fundamental en la ciencia de los materiales, la química y la metalurgia, ya que proporciona información crucial sobre la composición y las propiedades de los materiales.
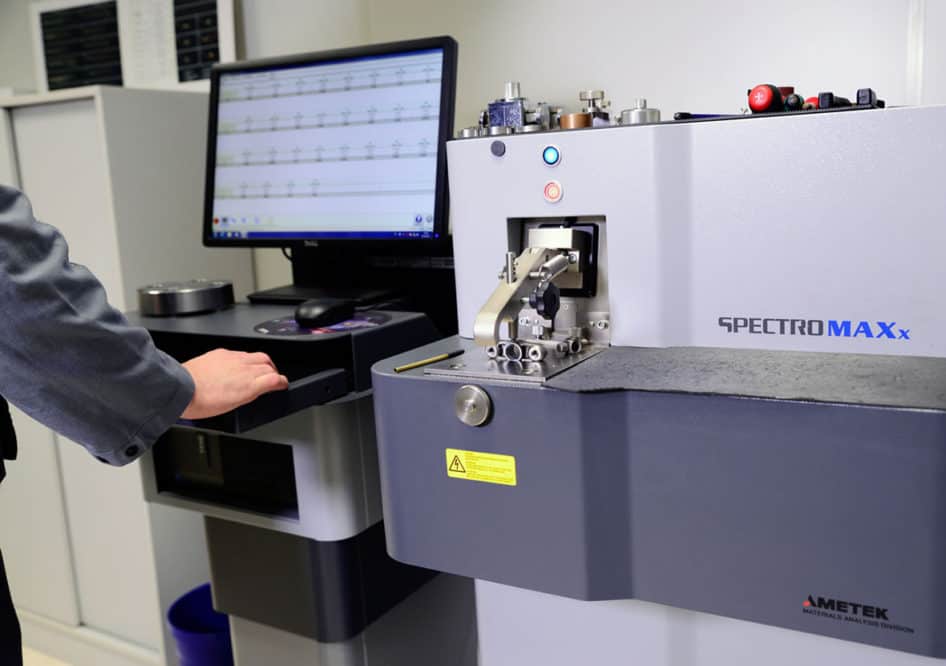
Existen diferentes métodos y técnicas para realizar el análisis de composición química, y la elección del método depende del tipo de material y de los elementos que se deseen analizar. Algunos de los métodos más comunes incluyen:
- Espectroscopia: Esta técnica se basa en la interacción de la luz con la materia. La espectroscopia puede ser de diferentes tipos, como la espectroscopia de absorción atómica (AAS), la espectroscopia de emisión óptica (OES) y la espectroscopia de fluorescencia de rayos X (XRF). Estas técnicas permiten identificar y cuantificar los elementos presentes en una muestra.
- Espectrometría de masas: Esta técnica se basa en la medición de la relación masa-carga de los iones generados a partir de la muestra. La espectrometría de masas permite identificar y cuantificar los elementos presentes, así como determinar la estructura molecular de compuestos orgánicos e inorgánicos.
- Análisis elemental: Este método se utiliza para determinar la cantidad de elementos específicos presentes en una muestra. Puede incluir técnicas como la titulación, la gravimetría y la electroquímica.
- Microscopía electrónica de barrido (SEM): Esta técnica combina la observación microscópica con el análisis químico. Permite obtener imágenes de alta resolución de la muestra y realizar análisis de composición química puntual o mapeo elemental.
- Espectroscopia de resonancia magnética nuclear (RMN): Esta técnica se utiliza principalmente para el análisis de compuestos orgánicos. Permite determinar la estructura y la composición química de las moléculas.
El análisis de composición química es esencial en la investigación y el desarrollo de nuevos materiales, así como en el control de calidad de los materiales existentes. Permite verificar la pureza de los materiales, identificar impurezas o contaminantes, y evaluar la conformidad con las especificaciones y los estándares requeridos.
Principio del ensayo
El análisis de composición química se realiza para determinar la composición química del material de soldadura utilizado. Permite verificar si los componentes del material cumplen con las especificaciones requeridas y si están dentro de los rangos aceptables para una soldadura de calidad.
Normas del ensayo
Las normas comunes para el análisis de composición química son la norma ASTM E415 paraanálisis de metales y la norma ISO 14284 para la determinación de la composición química de materiales metálicos. El análisis de composición química asegura que los componentes del material de soldadura estén dentro de los límites aceptables y cumplan con las especificaciones requeridas para garantizar una soldadura de calidad.
Ensayo de Radiografía
El ensayo de radiografía, también conocido como ensayo por rayos X o ensayo por radiografía, es una técnica no destructiva utilizada para evaluar la integridad interna de un objeto o material. Este ensayo se basa en la capacidad de los rayos X o los rayos gamma para penetrar en la materia y producir una imagen radiográfica que revela posibles defectos, como grietas, inclusiones, porosidades o discontinuidades internas.
El objetivo principal del ensayo de radiografía es detectar y evaluar la presencia de defectos internos en un objeto sin dañarlo. Esto permite identificar posibles problemas de calidad o integridad estructural que podrían afectar el rendimiento o la seguridad del objeto.
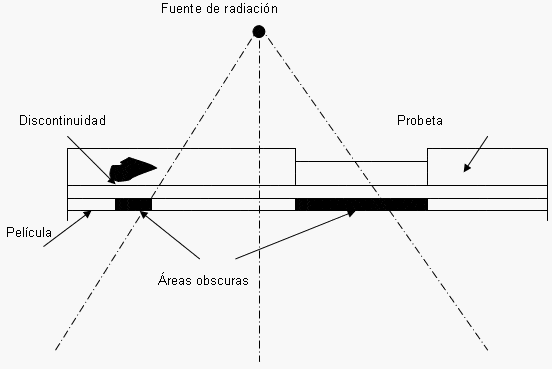
El ensayo de radiografía se realiza utilizando una fuente de radiación, como un tubo de rayos X o una fuente de rayos gamma, que emite radiación penetrante. Esta radiación atraviesa el objeto o material y alcanza una película radiográfica o un detector digital colocado en el lado opuesto. La radiación es absorbida de manera diferente por los diferentes materiales y estructuras internas, lo que resulta en una imagen radiográfica que muestra las variaciones de densidad y los posibles defectos.
La interpretación de las radiografías se realiza mediante la observación de las características de la imagen, como las áreas oscuras (donde la radiación ha sido absorbida) y las áreas claras (donde la radiación ha pasado sin ser absorbida). Los defectos internos, como las grietas o las inclusiones, aparecerán como áreas oscuras o como cambios en la densidad de la imagen.
El ensayo de radiografía es ampliamente utilizado en diversas industrias, como la industria aeroespacial, la industria del petróleo y gas, la industria de la construcción y la industria de fabricación de componentes metálicos. Se utiliza para inspeccionar soldaduras, fundiciones, estructuras metálicas, tuberías, componentes electrónicos, entre otros.
Este ensayo ofrece varias ventajas, como la capacidad de inspeccionar objetos de gran tamaño o de formas complejas, la detección de defectos internos difíciles de detectar visualmente y la posibilidad de realizar inspecciones sin dañar el objeto. Sin embargo, también tiene algunas limitaciones, como la necesidad de equipos especializados y personal capacitado, la exposición a radiación ionizante y la dificultad para detectar defectos superficiales o muy pequeños.
Principio del ensayo
El ensayo de radiografía es una prueba no destructiva que se utiliza para detectar defectos internos en una soldadura, como porosidades, fisuras o inclusiones. Se utiliza una fuente de radiación y una película o un detector digital para capturar una imagen de rayos X o gamma de la soldadura.
Normas del ensayo
Las normas comunes para el ensayo de radiografía son la norma ASTM E164 para radiografía industrial y la norma ISO 17636 para la radiografía de materiales metálicos. El ensayo de radiografía permite la detección de defectos internos en una soldadura sin dañarla. Los requisitos dependen de los estándares establecidos y las especificaciones del proyecto.
Estas pruebas de laboratorio son solo algunas de las muchas utilizadas en el proceso de soldadura. Es importante tener en cuenta que la selección de las pruebas adecuadas depende del tipo de soldadura, el material utilizado y las especificaciones del proyecto. Además, es esencial contar con personal capacitado y equipos adecuados para realizar estas pruebas de manera precisa y confiable.
En conclusión, las pruebas de laboratorio desempeñan un papel fundamental en el aseguramiento de la calidad en el proceso de soldadura. Estas pruebas permiten identificar posibles defectos, evaluar la resistencia y la integridad de las uniones soldadas, y garantizar que se cumplan los estándares establecidos. Al invertir en pruebas de laboratorio adecuadas, las industrias pueden asegurarse de que sus estructuras y productos finales sean seguros, confiables y de alta calidad.